💼 See What I Build | ⚡ Open to Full-Time & Startup Opportunities | 🔧 Let’s Collaborate on Freelance Projects
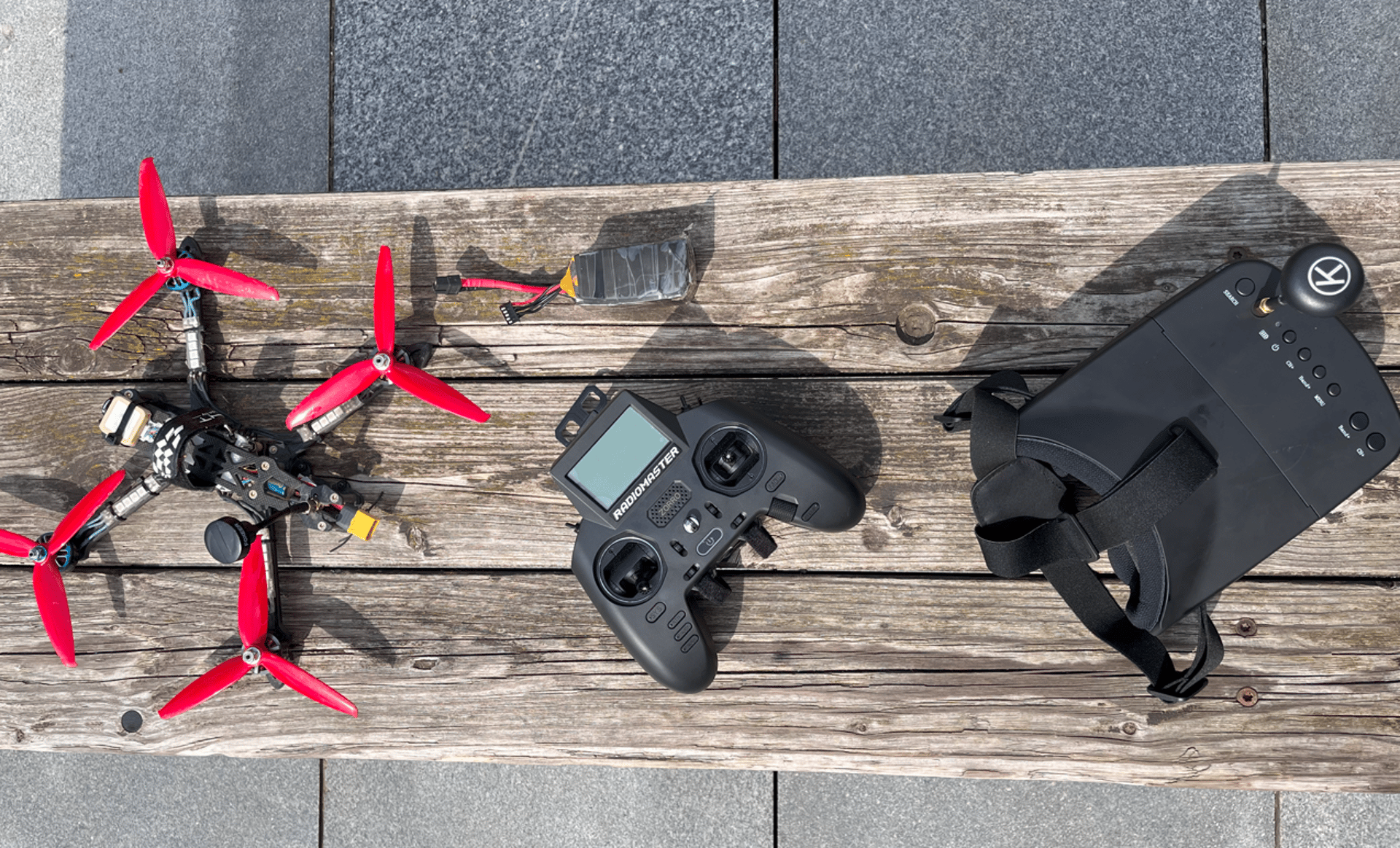


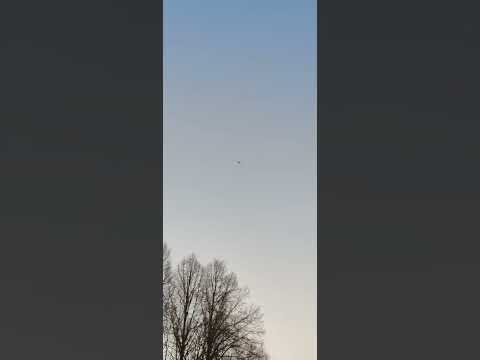
Return to Launch Testing
We are conducting altitude drop testing on a DIY drone project to assess its stability and reliability in real-world scenarios. During this testing, the drone is dropped from a certain height and its behavior is observed as it falls under the influence of gravity. Our drone is equipped with the Speedybee Stack microcontroller F405 V3, BLDC motors 2500kv, and a 5-inch freestyle frame type with an operation range of 1.2. When the drone reaches a certain point during its freefall, the engines are suddenly turned on, and its stabilization system takes over to prevent a crash. The goal is to make sure the drone can stabilize itself within a vertical range of approximately 100m. We are also working on incorporating autonomous functionalities such as image detection and recognition to enhance the flight experience. Our team is implementing an RTL (return to launch) feature that allows the drone to automatically return to its starting point in case of an emergency, as well as an ambient landing feature that helps the drone land safely even in challenging weather conditions.
"GPS Hold, a cutting-edge technology that enables your drone to maintain its position in the sky with unparalleled precision. This feature leverages the power of global positioning satellites to lock your drone's location, ensuring it remains stable and hovers in place, even in the face of wind and other external forces. Whether you're capturing breathtaking aerial footage or need your drone to stay put for a specific task, GPS Hold provides you with the confidence and control you need. Say goodbye to manual adjustments and hello to worry-free hovering with GPS Hold technology!"
Positioning Hold
High Altitudes
Gaining high altitudes with a drone is a complex feat that hinges on a combination of crucial factors. Firstly, the drone's propulsion system must be powerful, typically utilizing electric motors or, for larger drones, gas-powered engines, to generate the necessary thrust against gravity. The drone's aerodynamic design plays a significant role in reducing air resistance, with streamlined bodies and efficient rotor blades enhancing its climbing efficiency. Keeping the drone as lightweight as possible is essential, as less weight means less energy required for lift. High-capacity lithium-polymer or lithium-ion batteries are needed to provide the energy for sustained flight at high altitudes. Altitude control systems, equipped with barometric sensors and GPS, help maintain stability and ensure the drone doesn't lose control during the ascent. Ideal weather conditions are favorable for high-altitude flights, as wind and temperature can impact performance. Regulatory restrictions should also be considered, as aviation authorities often set limits on maximum drone altitudes. Additionally, safety measures, such as return-to-home functions and failsafes, are crucial for a well-planned ascent and descent strategy. High-altitude drone flights can yield valuable data, requiring monitoring systems and sensors for data collection and analysis throughout the flight. In essence, achieving high altitudes with a drone demands a harmonious blend of robust hardware, thoughtful design, meticulous planning, and strict adherence to regulations, all while maintaining safety and control.
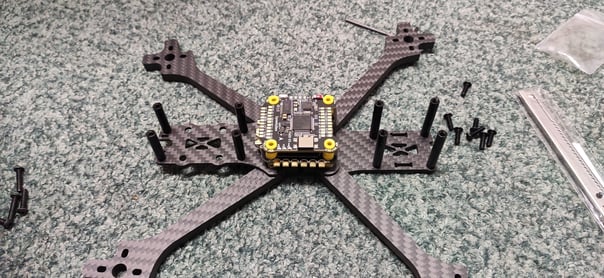
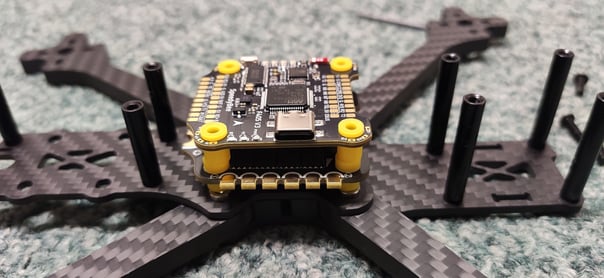
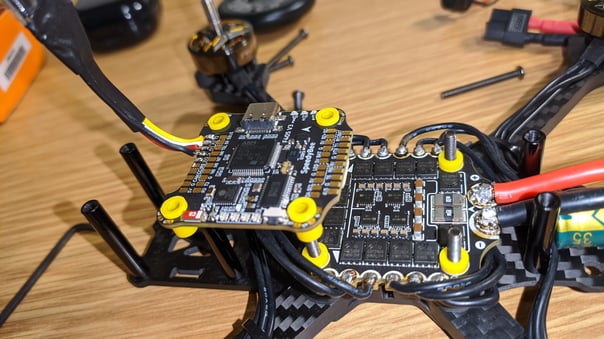
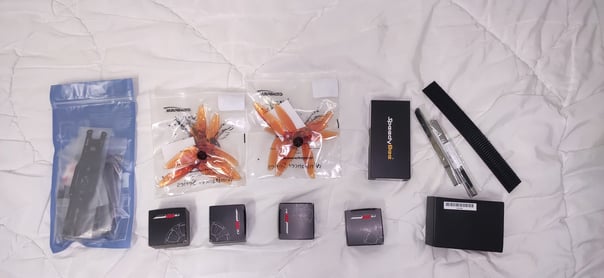
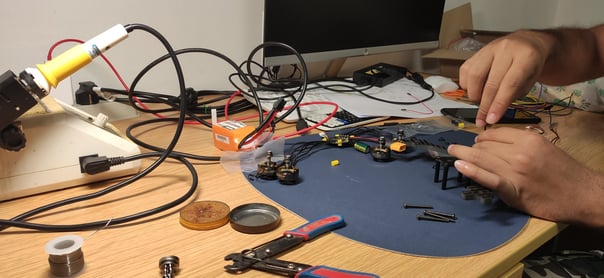
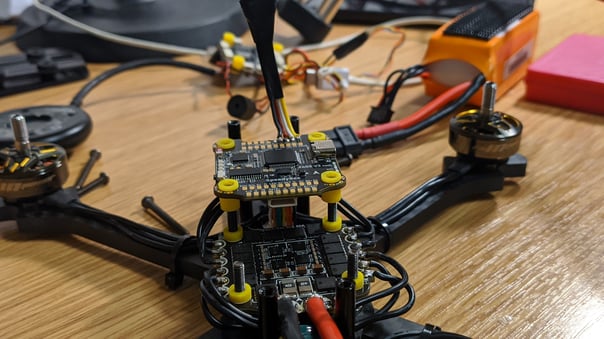
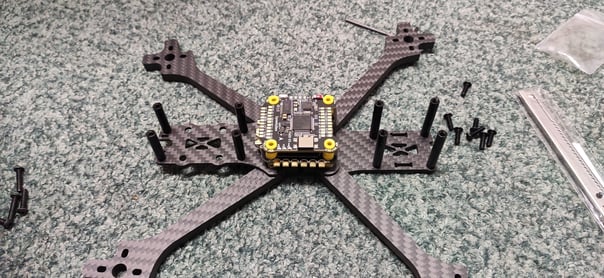
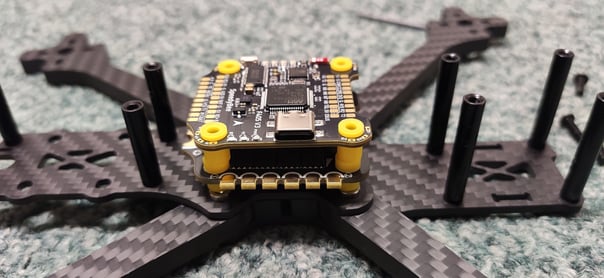
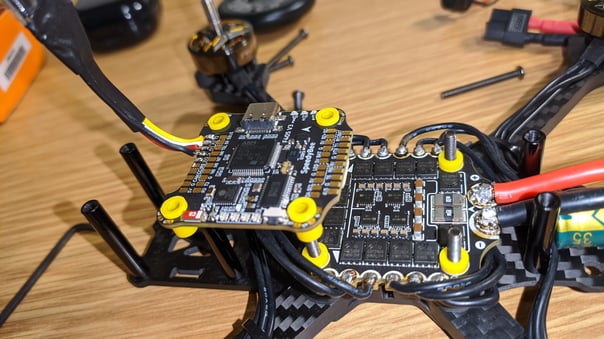
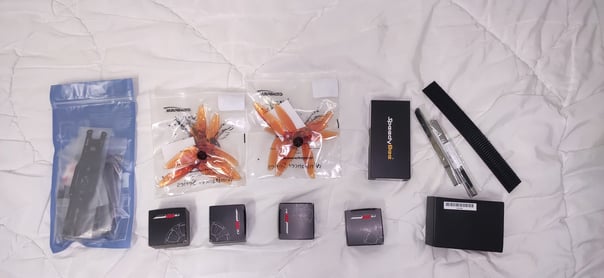
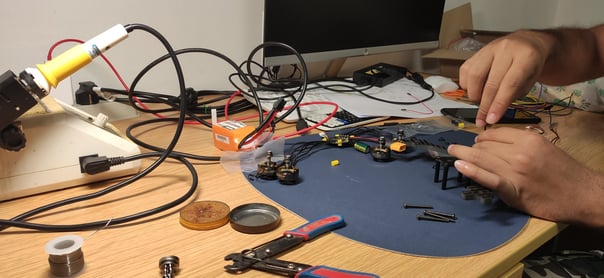
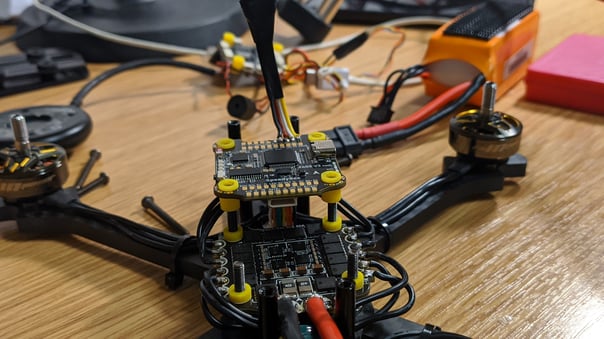

Fastest Drone Test ....120Km/hr
The project involves the design and fabrication of a high-speed drone with specific components, including four 2500kv BLDC motors, a 1-Speedybee 30X30 F405V3 processor, and a 16-bit 40Amp ESC board. The drone is constructed with an X frame configuration for stability, and the frame and motor mounts are 3D printed using materials like carbon fiber or nylon. After assembly and careful wiring, the drone is programmed using Python and the DroneKit library to implement stable flight dynamics. Additionally, the flight controller firmware, INAV, is configured for autonomous applications. Rigorous testing is carried out in controlled environments, gradually pushing the drone's speed to verify its capability to reach 120 km/hr. Fine-tuning and parameter adjustments are made to optimize the drone's speed and overall flight performance. It's essential to emphasize that safety measures and compliance with local regulations are paramount when working with high-speed drones to ensure responsible and safe operation.
• Design in SolidWorks and Fabricated X Frame with 3D printing Technology. Powered with 4-(2500kv)BLDC Motors with 1-Speedybee 30X30 F405V3 Processor integrated with 16-bit 40Amp Esc Board.
• Programmed with Python Programming Language by using DroneKit Library Extension for implementing stable flight dynamics.
• Also configured flight controller firmware (INAV) for Autonomous application.
• Currently working on human body posture recognition for drone movement via image recognition using Companion Computer as a Raspberry pi for Neural network implementation.